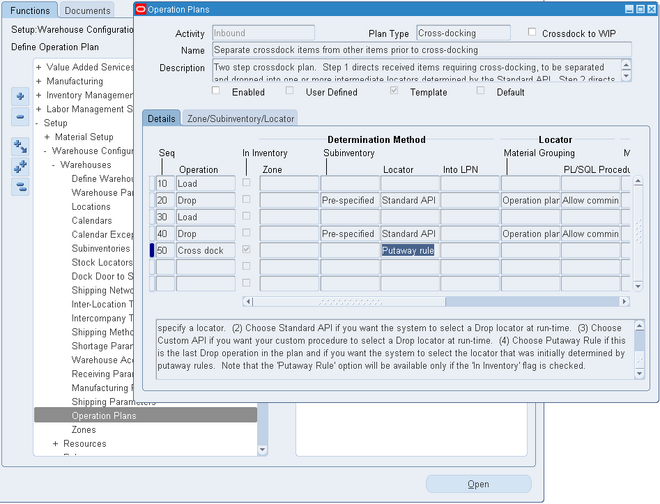
Operation plans define the material movement path and the sequence of operations to perform to complete an activity. You can use both inbound and outbound operation plans. You can create inbound Operation plans using the following inbound operation plan types:
- Standard: Standard operation plans apply to any move order lines that does not require inspection, or was not crossdocked. A standard operation plan can end in a receiving or inventory locator. It can also traverse multiple receiving and inventory locators. You cannot follow a drop to an inventory locator by a drop to a receiving locator, because once you drop material to an inventory locator, it is delivered to inventory.
- Inspect: Inspect operations plans apply to move order lines that have the Inspect Required flag set. The inspect step is the last step in the operation plan. Inspect operation plans do not allow drops to inventory locators.
- Crossdock: Crossdock operation plans apply to crossdocked move order lines. The crossdock step is the last step in the operation plan. The crossdock step implies a load and a drop to a staging locator. The drop operation before a crossdock operation does not happen in inventory.
- Set up Zones: If you choose to segregate your material by zones, you must create zones.
- Set up Operation Plan Assignment Rules: You must set up operation rules in the Rules window to tie your operation plans to your system rules.
1.1 Select a Plan Type from the list of values. You choices are Standard, Inspection, or Crossdocking.
1.2 Enter a name for the operation plan in the Name field. Optionally, enter a description for the operation plan in the Description field.
1.3 Select the Crossdock to WIP check box to use this operation plan to crossdock items to WIP instead of for outbound shipment.
2.1 Enter the first sequence number in the Sequence field. The operations performed within an operation plan follow the ascending sequence in which you define the operations.
2.2 Select Load from the Operation list of values. The first operation in all operation plans must be Load. The next sequence number defaults in the sequence field and Drop automatically populates in the Operations field.
3.1 Optionally, select the in Inventory check box. You can select this check box only if your operation plan type is Standard. Selecting this check box transfers the material to inventory at this step in the operation plan. All subsequent steps have this check box checked by default.
3.2 Locator determination method:
This is a mandatory field and you can set it for Drop operations only.
Select the determination method. You are required to enter a locator determination method, and optionally can enter a zone, subinventory, or Into LPN method. The determination methods are as follows:
• Prespecified: If you choose prespecified, you can enter the subinventory, locator, and zone where you would like to drop the material. This is the only determination method for subinventories and zones.
• Standard API- Standard API- If you choose Standard API as the locator determination method, you invoke an API that determines the locator. If you choose Standard API for locator, you must enter a pre-specified subinventory
or zone. You can also choose Standard API as the LPN determination method.
• Custom API- If you choose Custom API as the locator or LPN determination method, you provide the PL/SQL API. The API needs to conform to the signature as the seeded standard API and registered via Register custom API
concurrent program.
3.3 If you selected Standard API as the locator determination method, select a Locator Material Grouping method from the list of values. The available choices are as follows:
• Operation Plan Type: If you select Operation Plan type, the system derives the locator grouping method from the operation plan type such as inspection, Standard, or Crossdocking.
• Destination Subinventory: This is the final inventory destination subinventory the putaways rule suggests.
• Destination Locator: This is the final inventory destination locator the putaway rule suggests.
3.4 If you selected Standard API or Custom API as the locator determination method,
enter a PL / SQL procedure. The available choices for Standard API are as follows:
• Locator Determination with Item
• Locator Determination without Item
3.5 If you selected an LPN Determination method, select an LPN Material grouping method from the list of values. The available choices are:
• Operation Plan Type: If you select Operation Plan type, then the system derives the locator grouping method from the operation plan such as inspection, Standard, or Crossdocking.
• Destination Subinventory: This is the final inventory destination subinventory the putaway rule suggests.
• Destination Locator: This is the final inventory destination locator the putaway rule suggests.
3.6 If you selected an LPN Determination method enter a PL / SQL procedure in the Into LPN fields. The available choices for Standard API are as follows:
• Locator Determination with Item
• Locator Determination without Item
4.1 Select the Zone / Subinventory / Locator Tab.
4.2 Optionally, if your plan type is Inspect, or Crossdocking, enter the Inspect or Crossdocking sequence. In an Inspect or Crossdocking plan, this is the last operation.
4.3 If you entered crossdock in the previous step, select a Crossdock Method to link the crossdock operation plan to an outbound operation plan. The choices are:
• LPN based consolidation in staging lane within deliveries
• Locator based consolidation in consolidation locator within deliveries
• LPN based consolidation locator within deliveries
• Direct consolidation in staging lane within delivery
• LPN based consolidation in staging lane across deliveries
• Direct consolidation in staging lane across deliveries
• LPN based consolidation in consolidation locator across deliveries
• Locator based consolidation in consolidation locator across deliveries
4.4 Select Enabled to enable the operation plan.
Outbound operation plans
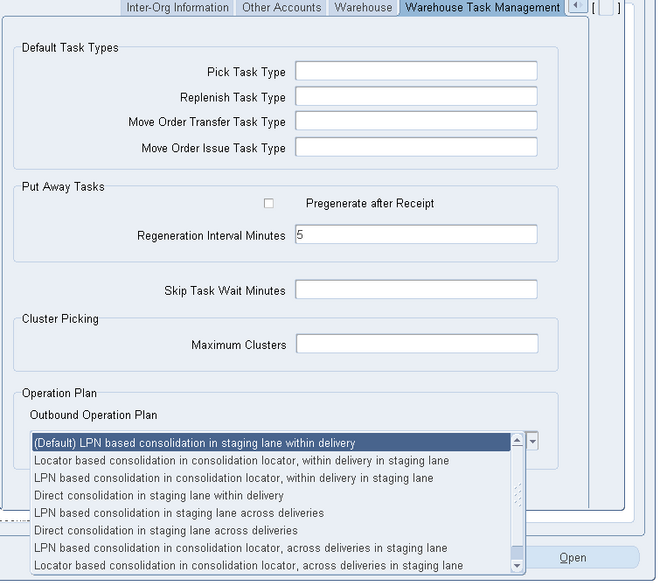
Eight seeded outbound operation plans are available, they are:
- Direct consolidation in staging lane across deliveries
- Direct consolidation in staging lane within delivery
- LPN based consolidation in staging lane within delivery
- LPN based consolidation in staging lane across deliveries
- LPN based consolidation in consolidation locator, across deliveries in staging lane
- LPN based consolidation in consolidation locator within delivery in staging lane
- Locator based consolidation in consolidation locator, across deliveries in staging lane
- Locator based consolidation in consolidation locator within delivery in staging lane.
0 comments